Was uns antreibt
Kürzere Produktlebenszyklen und kleine Stückzahlen stellen große Herausforderungen an die moderne Produktionstechnik. In der Optikfertigung kommen hohe Qualitätsanforderungen und der Einsatz komplexer, mehrstufiger Prozesse hinzu. Um diesen Herausforderungen zu begegnen, bedarf es automatisierter und selbstoptimierender Systeme.
In PhoenixD werden diese mittels virtueller Modelle realisiert, an welchen die optischen Bauteileigenschaften bereits während der Fertigung simuliert werden können. Anhand dieser Simulationen können sowohl einzelne Fertigungsprozesse als auch die Prozessketten angepasst werden.
Zum Erstellen der virtuellen Modelle ist umfangreiches Wissen über das in der Fertigung befindliche Bauteil notwendig. Dazu müssen zum Beispiel im Prozess wirkende Kräfte gemessen werden. Zudem werden Aktoren zum Anpassen der Prozesse benötigt.
Hierzu wird in der Arbeitsgruppe M4 ein magnetisch gelagerter Linearaktor entwickelt. Ähnlich wie bei einer Magnetschwebebahn (Transrapid) schwebt der Bauteilhalter und kann präzise in allen Raumrichtungen ausgerichtet werden. Die wirkenden Kräfte können präzise gemessen und angepasst werden. Der Aktor ist somit ideal zur Erfassung und Anpassung von einzelnen Fertigungsprozessen geeignet.
Damit darüber hinaus eine Anpassung gesamtheitlicher Prozessketten gelingt, müssen alle zum Einsatz kommenden Produktionsprozesse flexibel und modular miteinander Verknüpft werden. In der Arbeitsgruppe M4 wird erforscht, wie ein solches Fertigungssystem aufgebaut werden muss.
Unsere Forschungsarbeit
Die adaptive Fertigung in PhoenixD sieht vor, dass die Fertigungsgenauigkeit etablierter Fertigungsmethoden durch eine Zustandsrückführung und Parameteranpassung im Prozess (Qualitätsregelkreis) gesteigert wird. Hierdurch können Bauteile sowohl präzise als auch produktiv und somit kostengünstig gefertigt werden.
Ein Fertigungsverfahren mit besonders hoher Produktivität stellt zum Beispiel das in Arbeitsgruppe M2 – Additive/Subtraktive Fertigung erforschte Flexodruckverfahren dar. Der Ansatz des Qualitätsregelkreises bedingt, dass der Zustand im Prozess durch eine Sensorik erfasst werden kann. Zur Anpassung der Prozessparameter bedarf darüber hinaus einer entsprechenden Aktorik.
Zu diesen Parameteranpassungen zählen die Druckkraft zwischen Druckrolle und Substrat sowie der Ausrichtung des Substrats gegenüber der Druckrolle. In den am Markt verfügbaren Flexodruckmaschinen gibt es momentan jedoch keine Möglichkeit, diese Parameteranpassungen während des Druckprozesses vorzunehmen.
In Arbeitsgruppe M4 wird in diesem Zusammenhang ein flexibel einsetzbarer Linearaktor mit langem Verfahrweg in X-Richtung und elektromagnetischer Führung erforscht (siehe Abbildung 1). Die Führung besteht aus acht am Schlitten montierten Elektromagneten, die auf der Reluktanzkraft basieren Die Luftspalte zwischen den Magneten wird mit Wirbelstromsensoren erfasst. Zusätzlich erfolgt eine Messung der magnetischen Flussdichte mit Hallsensoren.
Mit der magnetischen Führung kann der Aktuator neben einer Linearbewegung auch eine Feinpositionier in die verbleibenden fünf Freiheitsgrade (zwei translative und drei rotative) ausführen. Aus dem Luftspalt und Spulenstrom der Magnete sowie der magnetischen Flussdichte lassen sich zudem die Lagerkräfte abschätzen, aus denen anschließend die Prozesskräfte abgeleitet werden können. Die Forderung nach sensorischen und aktorischen Fähigkeiten ist somit erfüllt.

Die eingesetzten Reluktanzkraftaktoren zeichnen sich gegenüber auf der Lorentzkraft basierenden Aktoren durch eine höheren Kraftdichte aus. Ihr instabiles Systemverhalten und nichtlineares Kennfeld setzt jedoch eine performante aktive Kraftregelung voraus. Eine Herausforderung hierbei ist die durch die aktive Regelung bedingte Totzeit zwischen einer messbaren Positionsabweichung und der entsprechenden Kraftanpassung der Magnetlager.
Um eine geringe Totzeit zu erreichen, wird die Stromregelung daher auf einem performanten Rapid-Prototyping-System durchgeführt. Die Stromsteller verwenden verlustarme Silicium Carbid (SiC) Halbleiter. Durch diese Maßnahmen konnte die Totzeit der Regelung gegenüber den typischen industrienahen Regelungssystemen in magnetisch gelagerten Werkzeugmaschinen bereits um 80 Prozent reduziert werden (siehe Abbildung 2).
Momentan wird der Linearaktor aufgebaut und soll in 2021 in Zusammenarbeit mit Taskgroup M2 in Kombination mit einem Flexodruck-Modul eingesetzt werden. Danach ist ein Einsatz in weiteren Fertigungsverfahren ist geplant, beispielsweise in der Montage (Arbeitsgruppe M5 – Optikmontage und –handhabung) und dem Heißprägen (Arbeitsgruppe M3 – Oberflächenpolierung und -beschichtung und optische Elemente: Forschung zu integrierten mehrschichtigen 2D-Oberflächenoptiken). Die durch den Aktor zur Adaption befähigten Fertigungsprozesse stellen zukünftig einen zentralen Bestandteil des Smart Manufacuring Grids (SMG) dar.

Weitere Arbeiten in der Arbeitsgruppe beschäftigen sich mit den Anforderungen an das SMG bezüglich der Modularität und Rekonfigurierbarkeit der Prozessketten hinsichtlich der Produktdiversitäten und den hohen Qualitätsanforderungen bei optischen Bauteilen. Die Anforderungen werden durch eine flexible Integration verschiedener Prozesstechnologien zur Herstellung von Bauelementen der Optoelektronik erfüllt.
Die dafür benötigten Betriebsmittel werden unter Berücksichtigung ihrer technischen und produktionslogistischen Anforderungen, die sich aus den zu fertigenden optischen Komponenten ergeben, in ein wandlungsfähiges Gesamtkonzept überführt (siehe Abbildung 3).
Im Zuge der Erstellung eines ganzheitlichen Produktionskonzepts werden Lösungsräume für die einzelnen Prozesskonstellationen geschaffen, mithilfe deren effiziente und aufeinander abgestimmte Logistikkonzepte abgeleitet werden können. Parallel zur technischen Auslegung des SMG wird ein Modell zur digitalen Abbildung der Produktion erstellt, durch das unterschiedlichste Fertigungsszenarien im Ablauf simuliert werden können. Die durch ein virtuelles Modell generierten Daten können im Wesentlichen einen Informationsvorteil für die Produktionsplanung bieten und für Anpassungen im Ablauf verwendet werden. Zusätzlich sollen Methoden entwickelt werden, die einen direkten Transfer des Wissens aus den Ablaufsimulationen auf dem Shopfloor ermöglichen sollen.

Ansprechpartner
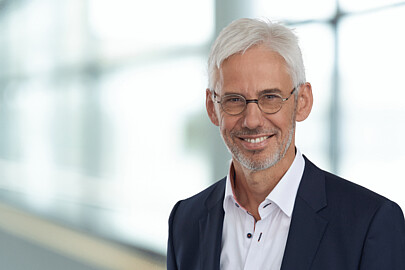
30823 Garbsen
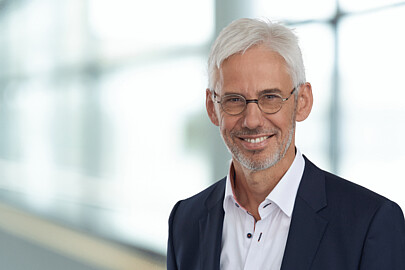
30823 Garbsen