Our Motivation
Shorter product life cycles and small quantities pose significant challenges to modern production technology. In optics production, there are also high-quality requirements and the use of complex, multi-stage processes. To meet these challenges, automated and self-optimising systems are required. In PhoenixD, these are realised employing virtual models, which can already simulate the optical component properties during the process. Based on these simulations, both individual manufacturing processes and process chains can be adapted.
To create virtual models, extensive knowledge about the component being manufactured is of particular importance. For example, forces acting in the process must be measured. In addition, actuators must adapt the processes. For this purpose, the Task Group M4 develops a magnetically supported linear actuator. Like a magnetic levitation train (Transrapid), the component holder levitates and can be precisely aligned in all spatial directions. The acting forces can be precisely measured and adjusted. The actuator is thus ideally suited for measuring and adjusting during the process. All production processes used must be linked flexibly and modularly with each other to adapt overall process chains. The members of Task Group M4 are researching how to set up such a production system.
Our Research
Adaptive manufacturing in PhoenixD enables that the manufacturing accuracy of established manufacturing methods increases through state feedback and parameter adjustment (quality control loop). This instant quality control leads to a precisely and productively, and thus cost-effectively, production of optical components y.
A manufacturing process with particularly high productivity is, for example, the flexographic printing process researched in Task Group M2 - Additive/Subtractive Manufacturing. The quality control loop approach requires that a sensor system can measure the status during the process.
Also, a corresponding actuator system is necessary to adjust the process parameters. These parameter adjustments include the pressure force between the printing roller and the substrate as well as the alignment of the substrate relative to the printing roller. In the flexo presses available on the market, however, there is currently no possibility to make these parameter adjustments during the printing process.
In this context, Task Group M4 is researching a flexible linear actuator with long travel in the X-direction and electromagnetic guidance (see Figure 1). The guidance consists of eight electromagnets mounted on the carriage, based on the reluctance force. The air gaps between the magnets are detected with eddy current sensors. Also, Hall sensors measure the magnetic flux density.
With the magnetic guidance, the actuator can perform fine positioning in the remaining five degrees of freedom (two translational and three rotational) in addition to linear movement. The bearing forces can also be estimated from the air gap and coil current of the magnets as well as the magnetic flux density, from which the process forces can subsequently be derived. Thus, the requirement for sensory and actuator capabilities is fulfilled.



A higher force density characterises the reluctance force actuators used compared to actuators based on the Lorentz force. However, their unstable system behaviour and non-linear characteristics require a high-performance active force control. One challenge here is the dead time caused by the active control between a measurable position deviation and the corresponding force adjustment of the magnetic bearings.
The current control is carried out on a high-performance rapid prototyping system to achieve a shorter dead time. The current controllers use low-loss silicon carbide (SiC) semiconductors. These measures have already reduced the control system's dead time by 80% compared to typical industrial control systems in machine tools with magnetic bearings (see Fig. 2).
The linear actuator is currently being set up and is to be used in 2021 in collaboration with Task group M2 combined with a flexographic printing module. After that, it is planned to use it in other manufacturing processes, such as assembly (Task group M5 - Optics Assembly and Handling) and hot stamping (Task group M3 - Surface Polishing and Coating and Optical Elements: Research on integrated multilayer 2D surface optics). The actuator's adaptive manufacturing processes will represent a central component of the Smart Manufacturing Grid (SMG) in the future.



Further work in the Task Group deals with the SMG requirements regarding modularity and reconfigurability of the process chains. The team looks into product diversities and the high-quality requirements for optical components. The requirements are met by a flexible integration of different process technologies for the production of optoelectronic components.
The operating resources required for this are transferred into a versatile overall concept, taking into account their technical and production logistical requirements, resulting from the optical components to be manufactured (see Fig. 3).
In creating a holistic production concept, solution spaces are created for the individual process constellations. From these different constellations, efficient and coordinated logistics concepts can be derived. Parallel to the technical design of the SMG, the researchers create a virtual model for the digital representation of production, which will simulate a wide variety of production scenarios.
The data generated by a virtual model can essentially provide an information advantage for production planning and be used for adjustments in the sequence. The team will also develop methods to enable the direct transfer of knowledge from the process simulations to the shop floor.



Contact
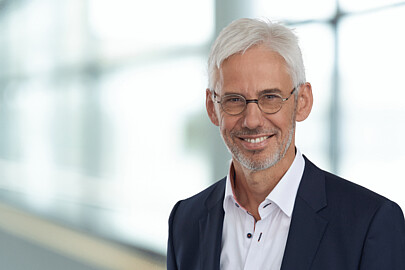
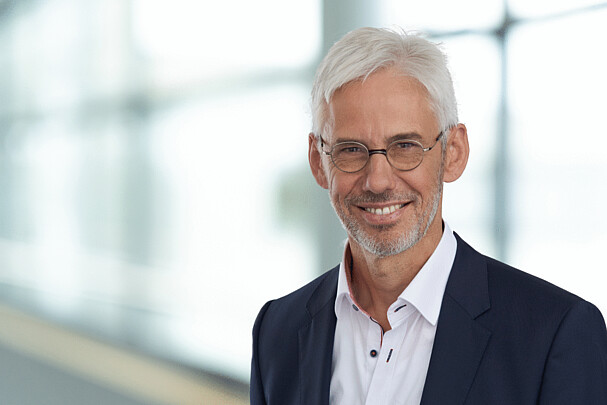
30823 Garbsen
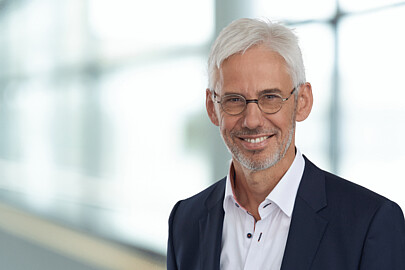
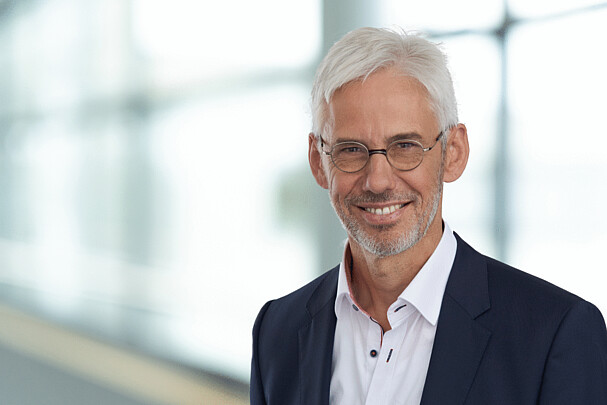
30823 Garbsen